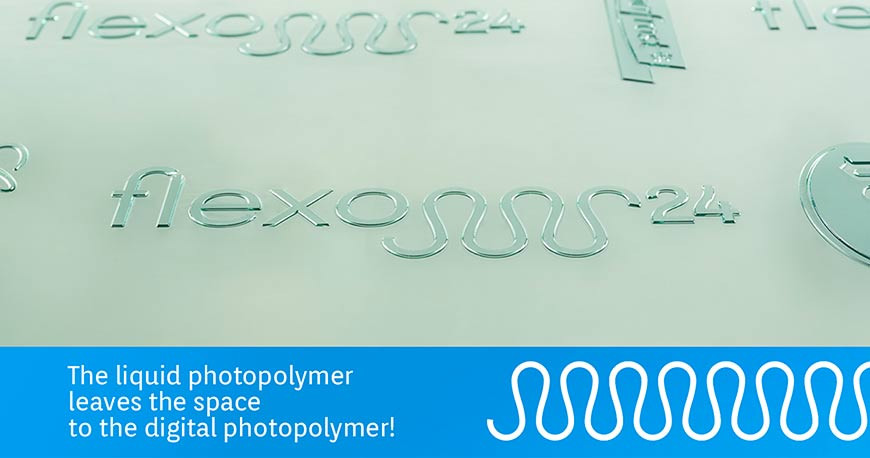
Liquid photopolymer gives way to digital plates!
Liquid photopolymer plates: goodbye! Go digital!
Liquid photopolymer or digital strong plates: what are the most significant differences and why going digital is now worthwhile!
Liquid photopolymer plates or digital plates? With the ever changing technology in the production of plates for flexible packaging and labels printing, flexo industry offers more and more varied solutions. A comparison between the two main available materials for the production of plates can’t be helped.
Liquid photopolymer plates and their features.
Liquid photopolymer plates were employed exclusively for printing on corrugated carton and are now almost completely being replaced by the engraved flexo plates. These offer improved results as to:
- versatility.
- quality in the reproduction of the printing elements.
Liquid photopolymer process.
These plates are produced by placing the film negatives onto the exposure unit and covering them with a transparent sheet. A roller evenly and uniformly spreads a liquid photopolymeric resin on top of the transparent cover sheet. The liquid photopolymer is enhanced by exposing the base side of the plate to ultraviolet light, hardening the photopolymer on the reverse side of the plate. Increasing or decreasing the exposure time varies the depth of penetration into the photopolymer of the radiation which varies the ultimate relief height of the plate. A second exposure to UV light from below (i.e., through the negative) hardens the photopolymer in the image areas of the plate. The non-image areas are left unexposed, soft and soluble. The exposed plate is removed from the exposure unit, and the cover film peeled from the exposed plate surface. The exposed plate is then sent to a washout unit which removes the unhardened photopolymer from the plate surface, leaving the exposed image areas in relief.
Digital plates and their features.
The imaging process of the photopolymeric digital plate starts with the CTP.
- A laser ablates the surface transferring texts and images from the PC directly to the digital plate.
- The plate is then exposed to the high intensity UV lights.
- This process enables the polimerisation of the engraved areas.
- After exposure, the following steps include first the automated washout, then drying and finishing of the plate under special UV lamps to restore its original rigidity and allow its use or printing.
Flexo digital plates are versatile and are available in many different versions to meet any specific market need. Digital plates can be suitable for water-based, solvent-based and UV inks or electron beam and offer optimum results to print on paper and paperboard, plastic film, aluminium and adhesive paper, carton, tissue. Find what is the most suitable plate for your print application.
PRO TIP
Digital photopolymer plates are the industrial benchmark for high quality flexo printing and allow a huge production capacity both for short and long print runs.
Advances in technology of digital plates.
These are the points to consider when selecting the right type of plate for a flexo print application:
- ink
- Substrate
- Quality
- Environment
- Production time and costs
Today, digital plates are the most suitable solution for flexo printing on any substrate and with any ink. As digital plates allow a huge potential in technology advances, many companies are steering their business to this product, optimising production time and costs and reducing their environmental footprint.
Try now the digital plate and become a customer of Flexo 24: order now your printing plates!