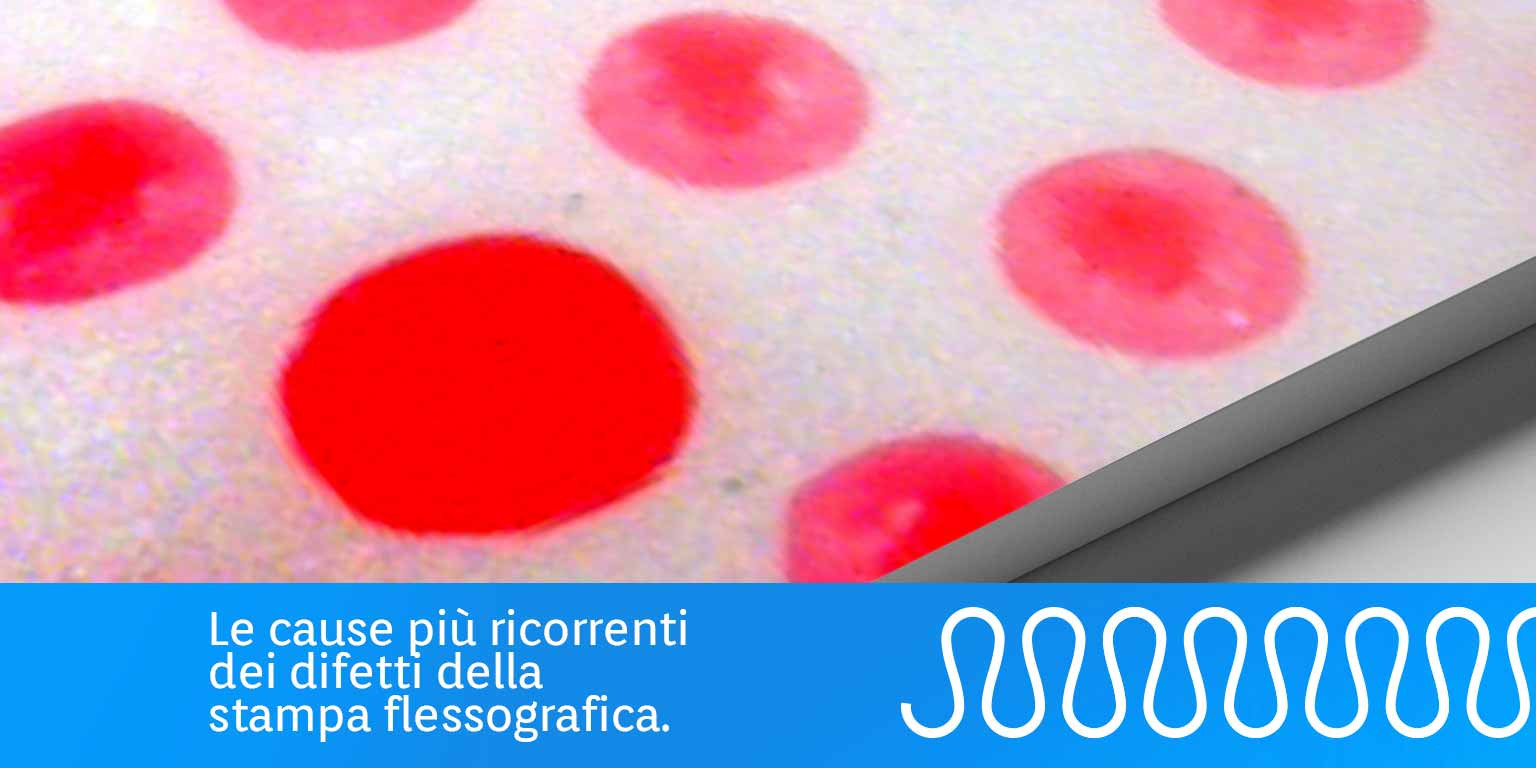
Errori di stampa flexo: le 12 cause maggiori e i rimedi!
Errori di stampa flexo: le 12 cause maggiori e i rimedi!
Errori di stampa flexo, di seguito i 12 errori più comuni e rimedi che si possono riscontrare nelle varie fasi della stampa flexo.
Riportiamo di seguito alcune tra le cause più ricorrenti dei difetti della stampa flessografica. Alcuni errori sono simili alla Stampa offset e simili alla rotocalco. È questa l'occasione per verificare i suggerimenti ai relativi rimedi. Da notare nel nome del difetto anche il corrispettivo in inglese perché nella terminologia tecnica è molto ricorrente la versione anglosassone, essendo tutta la tecnica flessografica nata alla fine dell’800 proprio negli Stati Uniti, come ben spiegato in questo articolo, link.
Ecco i primi dodici errori e rimedi:
- Adesione (Ahdesion)
- Impaccamento (Blocking)
- Fragilità della Stampa (Brittleness)
- Dot Dipping
- Grinze o pieghe (Creasing)
- Sporchi in stampa (Dark Dirty Print)
- Guadagno di punto (Dot Gain)
- Bordi Irregolari (Feathering)
- Schiuma (Foaming)
- Impastamento (Filling in)
- Effetto Fantasma (Ghosting)
- Capperini (Hickeys/Spots)
Qui l'elenco dei problemi che si possono riscontrare durante le varie fasi della stampa flessografica:
Adesione (Ahdesion). |
|
Questo fenomeno avviene quando la stampa non aderendo sufficientemente al supporto, si stacca. La stampa non supera i test meccanici dell’operatore quali il nastro adesivo, lo sfregamento o l’accartocciamento (wrinkle). |
|
CAUSE |
RIMEDI |
Inchiostro non adatto al tipo di supporto. |
Assicurarsi che l’inchiostro sia adatto al supporto. |
Inchiostro troppo diluito. |
Usare la viscosità corretta e assicurare la giusta quantità d'inchiostro stampato riducendo la diluizione.. |
Miscela di solventi sbagliata o debole. |
Verificare che i solventi usati siano quelli adatti per garantire una buona formazione dello strato di inchiostro sul supporto. |
Impaccamento (Blocking). |
|
Ovvero gli strati di materiale stampato si incollano tra di loro a causa della pressione, anche se moderata, per la variazione di temperatura. La gravità del danno, per almeno una delle due superfici, è visibile solo dopo la loro separazione. |
|
CAUSE |
RIMEDI |
L’inchiostro non asciuga sul supporto. |
Correggere la percentuale di solvente, utilizzare solventi ad evaporazione più rapida. Controllare gli essiccatori. |
L’inchiostro si asciuga sulla superficie e trattiene il solvente. |
Usare inizialmente meno calore. Ridurre la viscosità riducendo di conseguenza lo spessore dello strato di inchiostro. Controllare gli essiccatori. |
La bobina riavvolta è troppo calda. |
Ridurre la temperatura della bobina con un sistema di raffreddamento fino a raggiungere un valore compreso tra i 5°C rispetto la temperatura ambientale. Installare rulli di raffreddamento oppure ridurre la temperatura dell’essiccatore. |
Con la newsletter di Flexo 24 ricevi subito € 20,00 di sconto per il primo ordine superiore a € 199,00, e solo info utili. Iscriviti:
Fragilità della stampa (Brittleness). | |
Tra gli errori di stampa flexo questo errore è dovuto al trattamento non corretto, sia in fase di produzione che in quella di stampa, del cliché flexo. Rivedi quali sono le fasi della produzione delle lastre flessografiche nella pagina che abbiamo dedicato alla tecnologia. | |
CAUSE | RIMEDI |
Eccessivo calore o esposizione UV nel sistema di essiccazione o di polimerizzazione UV che causano un rilascio di umidità e plastificante dal supporto oppure dallo strato di inchiostro. | Controllare la temperatura della bobina. Ridurre il calore e /o aumentare il volume di aria nella camera di asciugamento. |
Cattiva aderenza. | Ridurre la potenza delle lampade UV. |
Dot dipping. | |
Questo fenomeno avviene quando alcuni punti incisi della lastra sono
troppo piccoli rispetto alla trama del rullo anilox, del
rullo inchiostratore. I punti incisi entrano nelle celle del rullo
inchiostratore, l’inchiostro non si deposita solo sulla parte superiore del
punto ma anche sulla spalla, trasferendo una quantità maggiore di inchiostro
sul supporto di stampa rispetto agli altri punti. | |
CAUSE | RIMEDI |
Anilox con lineatura troppo bassa rispetto alla lineatura di retinatura. | Usare anilox con lineatura più alta. |
Punti minimi della lastra irregolari con alcuni di dimensioni inferiori allo standard | Verificare la calibrazione della lastra. Ridurre la lineatura del cliché. Interrompere il punto minimo sul cliché, al minimo consentito dall’anilox utilizzato. |
Grinze o pieghe (Creasing). | |
Durante la fase di stampa si possono manifestare delle grinze, delle pieghe sul supporto. | |
CAUSE | RIMEDI |
Supporto difettoso. | Cercare di distendere le pieghe verso i bordi laterali della bobina del supporto con rulli distensori. |
Malfunzionamento della guida del nastro. | Controllare e pulire la guida del nastro. Posizionare la guida e le anime delle bobine in modo che essa si srotoli e arrotoli ad ugual distanza dalle estremità evitando spostamenti eccessivi. |
Macchina flessografica fuori allineamento. | Riallineare la macchina, specialmente i rulli. |
Sporchi in stampa (Dark Dirty Print). | |
È facilmente visibile per la quantità eccessiva di inchiostro trasferita sulla stampa e per il colore troppo saturo. | |
CAUSE | RIMEDI |
Eccessivo volume dell’anilox. | Scegliere un anilox con celle di volume inferiore. |
Viscosità dell’inchiostro non corretta. | Controllare la viscosità dell’inchiostro e mantenerla al valore corretto durante la tiratura. |
Dot gain (schiacciamento) eccessivo. | Regolare la pressione al livello minimo (kiss point) e/o utilizzare un biadesivo più morbido. |
Guadagno di punto (Dot gain). | |
L’errore è visibile per l’aumento dell’area dei punti retinati tra la lastra, il cliché inciso e la stampa. Da non confondere l'errore qui descritto con il valore di compensazione del punto di stampa, dot gain compensation. | |
CAUSE | RIMEDI |
Eccessivo volume d’inchiostro. | Ridurre il volume dell’anilox mantenendo il bilanciamento dei colori. |
Eccessivo spessore della lastra, del cliché oppure rigonfiamento della stessa. | Verificare che lo spessore della lastra sia da specifiche e controllare l'eventuale presenza di residui di solvente che creano rigonfiamenti. Nel caso sostituire la lastra. |
Biadesivo non corretto oppure presenza di bolle d'aria tra biadesivo e lastra. | Cambiare il biadesivo. Verificare la presenza di bolle d’aria sotto il biadesivo di montaggio ed eventualmente rimontare la lastra. |
Bordi irregolari (Feathering). | |
I bordi irregolari attorno ai grafismi stampati sono errori che si manifestano come conseguenza di una eccessiva pressione, causati generalmente da un eccessivo accumulo di inchiostro con aumento della superficie dei punti retinati dalla lastra alla stampa. | |
CAUSE | RIMEDI |
Unità di stampa con pressione non corretta. | Reimpostare la pressione tra tutti i rulli. |
L’inchiostro asciuga sulla lastra. | Pulire accuratamente le lastre. Aumentare la velocità della macchina. Rallentare l’asciugamento aggiungendo ritardanti all’inchiostro. Assicurarsi che i contenitori di inchiostro siano coperti. |
Impostazione non corretta del sistema di dosaggio dell’inchiostro | Ripristinare le regolazioni delle pressioni tra il rullo dosatore e il sistema di raclatura. |
Schiume (Foaming). | |
Questo errore avviene per l’eccessiva quantità di schiuma presente nell’unità di stampa, vasche o pompe dell’inchiostro. | |
CAUSE | RIMEDI |
Non corretto bilanciamento tra i solventi. | Aggiungere un solvente con alta percentuale di alcool per correggere la miscela. |
pH o viscosità non corrette. | Correggere il grado di pH e ridurre la viscosità. Aggiungere piccole quantità di prodotto antischiuma. |
Rapporto 1:1 tra anilox e rullo inchiostratore. | Ridurre il rapporto di rotazione del rullo inchiostratore. |
Impastamento (Filling). | |
È l’accumulo eccessivo di inchiostro sulla superficie ruvida del cliché e sulla spalla dei grafismi incisi che crea l’errore di impastamento. Esso si presenta specialmente in corrispondenza dei caratteri piccoli e dei retinati. | |
CAUSE | RIMEDI |
Quantità di inchiostro eccessiva. | Utilizzare un anilox con minor volume. |
Particelle di materiale pigmentato o estraneo. | Usare inchiostri ben miscelati e privi di particelle di grandi dimensioni. Assicurarsi che la pompa e le condutture degli inchiostri siano ben pulite. |
Carattere, grafica o retino non corretto. | Verificare che la grafica utilizzata sia idonea per la flessografia anche con le specifiche elencate in questo articolo dedicato alle caratteristiche per il pdf della flexo. |
Effetto fantasma (Ghosting). | |
È la presenza di una immagine duplicata più lieve riprodotta in una zona in cui non dovrebbe apparire. Di solito è un motivo ripetuto nella stampa. | |
CAUSE | RIMEDI |
La pompa dell’inchiostro è sottodimensionata rispetto al consumo di inchiostro richiesto dalle illustrazioni stampate o dalla camera racla. L’anilox non viene inchiostrato in modo adeguato al consumo. | Verificare l’efficienza della pompa oppure sostituirla con una più potente o aumentare il tempo di contatto tra l’inchiostro e l’anilox all’interno della camera racla con racle più distanziate per favorire la corretta re-inchiostrazione del rullo in rotazione. |
Viscosità dell’inchiostro troppo elevata per la pompa usata. | Controllare e regolare la viscosità dell’inchiostro. |
L’inchiostro si asciuga prima sull’anilox che sul supporto da stampare. | Con inchiostri a solvente il fenomeno potrebbe essere provocato a una viscosità troppo bassa. Una viscosità più elevata dovrebbe rallentare l’asciugamento sugli anilox. |
Capperini (Hickeys or spots). | |
Quando si presentano piccole macchie non volute stampate, di colore bianco, come "non colore", che circonda una piccola quantità d'inchiostro. | |
CAUSE | RIMEDI |
Polvere presente sul supporto che si trasferisce sulla lastra. | Se necessario, pulire la lastra e usare i dispositivi di pulizia e antistatici. |
Tiro dell’inchiostro eccessivo. | Rallentare o diluire l’inchiostro per ridurne il tiro (tack). |
Carta con patinatura poco ancorata. | Controllare con il produttore della carta. |
Inizia subito e diventa cliente Flexo 24: realizza i tuoi cliché!